Surface finishes
When a piece of fabric is removed from the loomMachine for weaving threads., it is rough and grey in colour. Finishing begins with washing the fabric and then often bleaching it to make it appear white. It is then ready for treatments that improve the appearance and function of the fabric.
Mechanical finishing
There are several mechanical finishes to improve appearance and texture:
- brushing - fabric is sent through a series of fine wire-toothed rollers, which raise the fibres giving the fabric a soft, fluffy surface which improves the insulation properties of the fabric
- calenderingA calender is a heated roller used to press fabric and paper. - sends fabric through heated, pressurised rollers that give the fabric a smooth, lustrous (shine) finish, used for upholstery fabric
- embossing - synthetic fabrics are sent through heated, engraved rollers which press the pattern texture into the fabric, called moir茅
Chemical finishing
Chemical finishing techniques are available to improve function and properties:
- mercerisingSodium hydroxide is added to the fibres making them swell to give a shiny appearance and soft touch. - cotton fibres are treated with a solution of sodium hydroxide, making them stronger, softer and more lustrous
- crease resistance - cellulose fibres, such as cotton, crease badly and treating the fabric with a resin-based finish reduces how much the fabric creases
- shrink resistance - to prevent wool fibres shrinking when washed they can be treated with chlorine, which removes the scales of the wool fibres that cause the shrinkage
- anti-static - synthetic fibres can be treated with chemicals to help decrease their water absorption, making them waterproof and prevent the build-up of static that makes fabric cling to itself
- stain resistance - a silicone-based spray can be used to prevent grease and dirt clinging to the fibres and is usually sprayed on after a product has been manufactured
- flame resistance - most fibres burn and could be a potential death hazard- by law upholstery fabric has to be treated with a flame-resistant finish
- water repellency - silicones (a tough synthetic material) are applied to a fabric鈥檚 surface to temporarily prevent water being absorbed by the fabric; PVC can coat the fabric to make it permanently water proof but doesn鈥檛 allow the skin to breathe
Dyeing
There are several different ways of dyeing fabrics:
- stock or yarn - dyes the fibres before they become fabrics
- piece - dyes pieces of fabric
- garment - dyes clothing once it is made
Dyeing usually takes place in large vatLarge container. before being heated and dried.
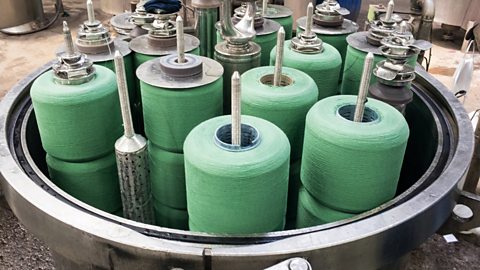
Printing
Commercial printing prints pattern onto the top surface of fabrics. There are a variety of printing methods available:
Screen printing
A screen with the stencil of the pattern has dye wiped over it to produce an accurate, repeatable print. A separate screen for each colour is required.
Roller printing
Roller printing can be used for long, striped patterns. A roller for each colour has a pattern embossedTo stamp a pattern onto a surface so that it stands out. on it. As the fabric passes through, the pattern is added.
Sublimation printing
sublimation inkA dye suspended in a liquid for printing on to hard surfaces. is printed onto coated paper. Once heated, the image is transferred onto fabric.
Digital printing
Digital printing allows fabric to be printed on directly from an inkjet head. It is expensive but offers a wide range of colours.
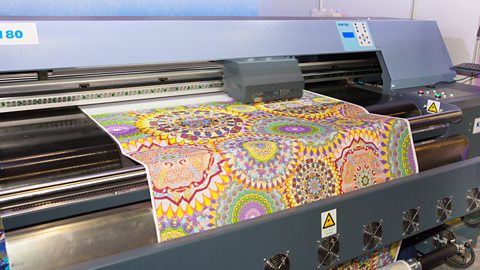